Digital twin vs digital shadow vs digital model: key differences explained
Choosing the right digital technology for smart manufacturing
In the world of Industry 4.0 and digital transformation, terms like digital twin, digital shadow, and digital model are often used interchangeably. However, they are not the same—each serves a different purpose in industrial automation and manufacturing simulation.
Understanding these differences is essential for manufacturers looking to optimize processes, reduce downtime, and implement smart factory solutions. But how can companies practically adopt these technologies without high costs and complexity?
With solutions like Visual Components, distributed by Flexcon, companies can easily integrate simulation, virtual commissioning, and digital twin technology into their production workflows.
Let’s break down the key differences and explore how simulation is the best starting point for manufacturers adopting digital twins.
What is a Digital Model?
📌 Definition: A digital model is a 3D representation of a product, system, or production layout. It can be static or animated, but it does not connect to real-time production data.
Where Are Digital Models Used?
- Conceptual design of new products
- Factory layout planning
- Basic manufacturing process simulation
Example: An automotive company creates a 3D model of an assembly line to test robotic movement. Yet, the model is isolated and does not reflect real-time production conditions.
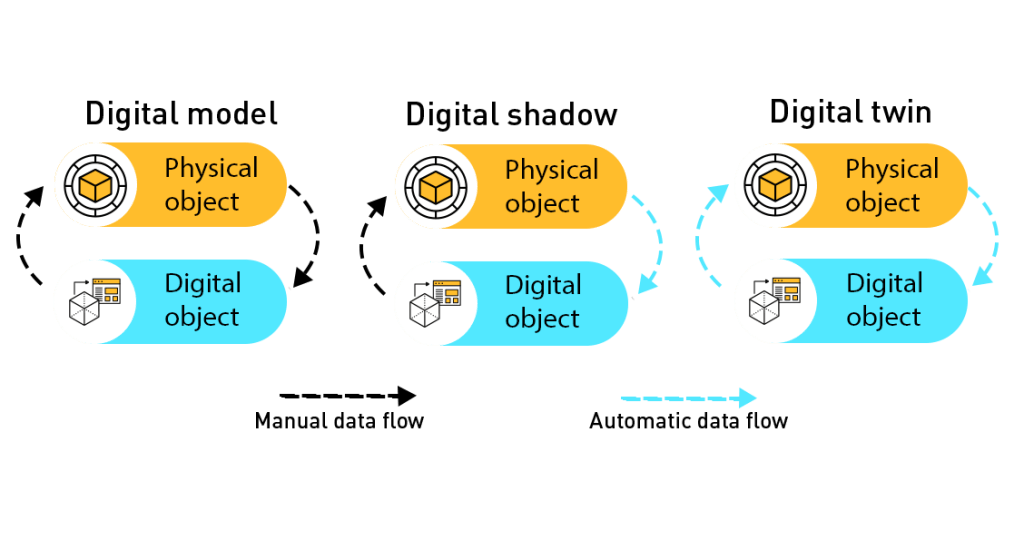
What is a Digital Shadow?
📌 Definition: A digital shadow is a virtual representation that automatically receives real-time data from its physical counterpart. However, this is a one-way data flow—it monitors the system but cannot control or optimize it.
Where Are Digital Shadows Used?
- Machine performance monitoring
- Production data collection
- Predictive maintenance planning
Example: A logistics company uses a digital shadow to track warehouse conveyor speeds and identify inefficiencies. Operators will manually adjust the system.
What is a Digital Twin?
📌 Definition: A digital twin is a real-time, bidirectional digital counterpart of a physical system. Unlike a digital shadow, it not only receives real-time data but also influences the physical system. This enables live process optimization, predictive analytics, and AI-driven automation.
Where Are Digital Twins Used?
- Virtual commissioning for automation validation
- Real-time process optimization
- AI-powered predictive maintenance
- Workforce training in simulated environments
Example: A pharmaceutical company uses a digital twin of its production line to automatically adjust machine speeds based on demand—reducing downtime and improving efficiency.
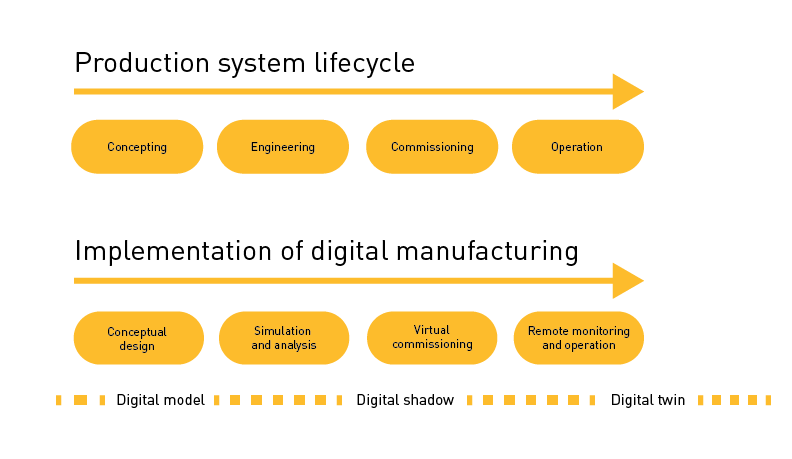
An image from Visual Components, clearly showing how the digital twin is an evolution of the digital shadow, enabling full integration into production processes, from design to remote monitoring.
Why digital twin is the future of smart manufacturing
Feature | Digital Model | Digital Shadow | Digital Twin |
---|---|---|---|
Data connection | ❌ None | ✅ One-way | ✅ Two-way |
Real-time updates | ❌ No | ✅ Yes | ✅ Yes |
Can influence physical system? | ❌ No | ❌ No | ✅ Yes |
Use cases | Conceptual design | Monitoring & reporting | Optimization & automation |
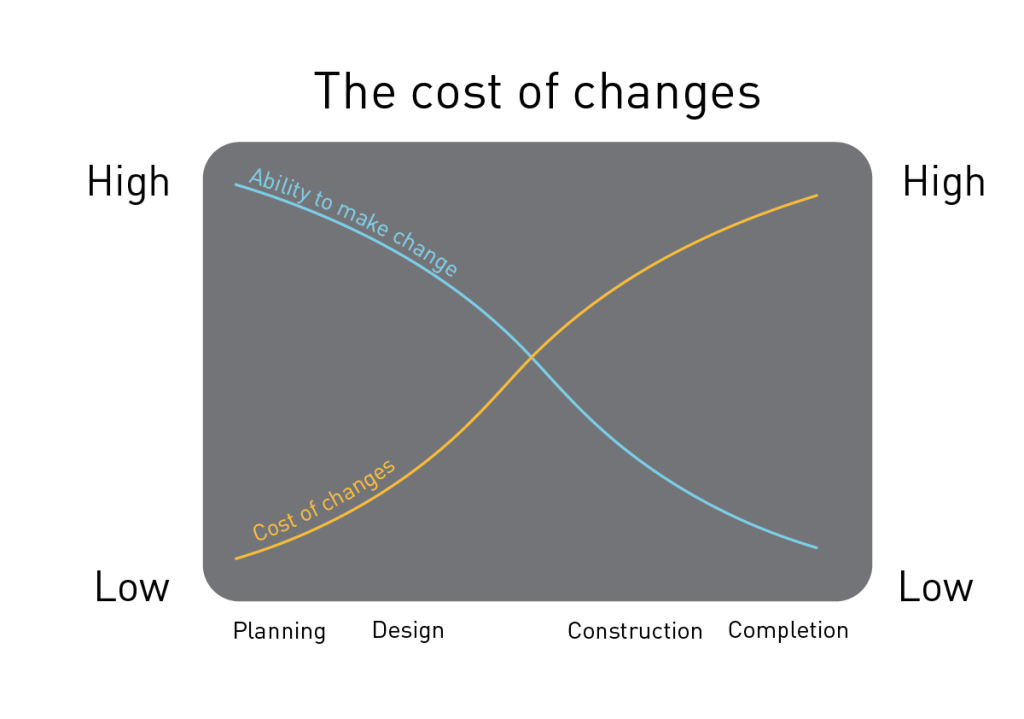
The earlier a company implements digital twins, the lower the cost of production changes.
Digital twin: start your journey with simulation.
Adopting a digital twin requires a structured and progressive approach. With Visual Components, you have an advanced tool for simulating and optimizing production processes, while Flexcon supports you throughout the entire integration process, ensuring a safe and scalable transition.
Here are the key steps for a successful implementation:
1️⃣ Start with 3D simulation → Validate layouts, processes, and automation strategies in a risk-free environment.
2️⃣ Use virtual commissioning → Test and refine automation systems before their physical deployment.
3️⃣ Integrate real-time data → Connect sensors and IoT to evolve from a digital shadow to a fully functional digital twin.
4️⃣ Leverage AI for optimization → Apply predictive analytics to minimize downtime and enhance efficiency.
By following this approach, you’ll be able to optimize production layouts before implementation, validate automated processes, reduce inefficiencies and downtime through simulation, and train operators in a virtual environment without impacting real production.
Contact Flexcon: take the first step toward a truly data-driven, optimized production system.
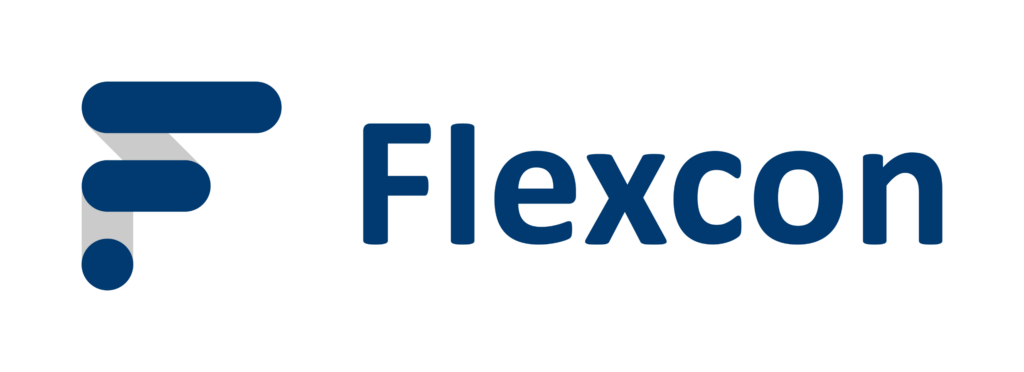